Comparison of Mounting Methods for Turning Slender Spindles
If one attempts to turn a spindle down to a smaller and smaller diameter, eventually one reaches the point where chatter marks begin to develop and further turning leads to increased chatter and possibly whipping of the spindle. The minimum diameter that can be achieved before this happens depends on several factors including the method used to mount the spindle. There have been posts from time to time comparing various mounting methods, but I have not seen any that give quantitative results. As an engineer (long retired), this intrigued me to the point that I decided to see if I could shed some light on the subject. I carried out a mathematical analysis of the problem based on standard engineering equations for beam deflection and followed it up with controlled experiments to try to confirm the calculations. An article, giving full details of the project can be found in the “ How-tos, Tips and Techniques” forum, but the main results are summarized below.
I compared five mounting methods, which are listed in order of increasing performance:
1. One end in chuck, the other free. 100%
2. Between centers—the most common method, and the standard of comparison here. 50%
3. One end in chuck, the other supported by a center. 59%
4. Both ends in chucks. 50%
5. Both ends in chucks and the spindle under tension. 50%
In each case, it was assumed that no other support was provided. (No steady-rest nor steadying hand wrapped around the spindle.) All results are based on a simple cylindrical spindle and will not apply exactly to arbitrary spindle profiles, although the ranking order will remain as shown. Mathematical analysis of Method 5 is impractical so only experimental results are presented and they are limited to one particular case. For each mounting method, there is a critical point along the spindle where deflection is greatest for a given tool force. The locations of these points are noted in the list above as a percent of the distance from the drive end to the outer end of the spindle.
The premise underlying the analysis was that for a given type of wood, spindle length and cutting tool and possibly other factors, chatter begins when the deflection of the spindle caused by tool pressure reaches a certain amount, independent of the mounting method used. On this assumption, mounting methods that yield higher stiffness will perform better than ones that yield lower stiffness. Furthermore, with this assumption, one can use well-known engineering beam deflection equations to calculate the relative minimum diameters that can be achieved for a given spindle length by the various mounting methods and, conversely, the relative lengths of the spindles that can be turned to a common diameter. The experiments were carried out to test this premise and, in fact, the test results seem agree quite well with the calculated ones as shown in the following figures. Note that these are relative results, with Method 2 being the standard.
Comparison of Relative Diameters Achievable
Comparison of Relative Lengths Achievable
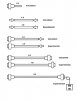
If one attempts to turn a spindle down to a smaller and smaller diameter, eventually one reaches the point where chatter marks begin to develop and further turning leads to increased chatter and possibly whipping of the spindle. The minimum diameter that can be achieved before this happens depends on several factors including the method used to mount the spindle. There have been posts from time to time comparing various mounting methods, but I have not seen any that give quantitative results. As an engineer (long retired), this intrigued me to the point that I decided to see if I could shed some light on the subject. I carried out a mathematical analysis of the problem based on standard engineering equations for beam deflection and followed it up with controlled experiments to try to confirm the calculations. An article, giving full details of the project can be found in the “ How-tos, Tips and Techniques” forum, but the main results are summarized below.
I compared five mounting methods, which are listed in order of increasing performance:
1. One end in chuck, the other free. 100%
2. Between centers—the most common method, and the standard of comparison here. 50%
3. One end in chuck, the other supported by a center. 59%
4. Both ends in chucks. 50%
5. Both ends in chucks and the spindle under tension. 50%
In each case, it was assumed that no other support was provided. (No steady-rest nor steadying hand wrapped around the spindle.) All results are based on a simple cylindrical spindle and will not apply exactly to arbitrary spindle profiles, although the ranking order will remain as shown. Mathematical analysis of Method 5 is impractical so only experimental results are presented and they are limited to one particular case. For each mounting method, there is a critical point along the spindle where deflection is greatest for a given tool force. The locations of these points are noted in the list above as a percent of the distance from the drive end to the outer end of the spindle.
The premise underlying the analysis was that for a given type of wood, spindle length and cutting tool and possibly other factors, chatter begins when the deflection of the spindle caused by tool pressure reaches a certain amount, independent of the mounting method used. On this assumption, mounting methods that yield higher stiffness will perform better than ones that yield lower stiffness. Furthermore, with this assumption, one can use well-known engineering beam deflection equations to calculate the relative minimum diameters that can be achieved for a given spindle length by the various mounting methods and, conversely, the relative lengths of the spindles that can be turned to a common diameter. The experiments were carried out to test this premise and, in fact, the test results seem agree quite well with the calculated ones as shown in the following figures. Note that these are relative results, with Method 2 being the standard.
Comparison of Relative Diameters Achievable
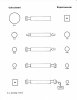
Comparison of Relative Lengths Achievable
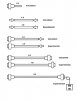