It took awhile to figure out, but I now know why the Beall buffing system mandrel doesn't seat fully in my Jet 1236 Morse taper (headstock). All of my drive centers have an area at the end of the taper where the diameter is smaller, like a rabbet at the end (see picture below). Inside the Morse taper, if probed with a dowel, the wall narrows via a bevel. Obviously, the rabbet on the drive centers clears this bevel and allows them to seat fully. Since the Beall is tapered all the way to the end, it bumps against the narrowing wall just a tiny smidge before the mandrel fully seats. So, there's just a little bit of play. I guess I'll have to grind down the butt end a little bit to solve it. Any tips?
[Calipers are there only to keep the drive center from rolling]
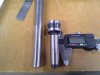
[Calipers are there only to keep the drive center from rolling]
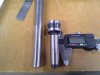