The shape and where in the tree the wood comes from is the mayor reason wood warps more or less, and yes some wood species will move more than others, a knot in a side of the blank can really make for twisting and warping, I have a couple pictures here that show the different reasons why these pieces did warp and twist.
Two pictures that show a more stable shape, one is once turned Poplar the other twice turned White Ash.
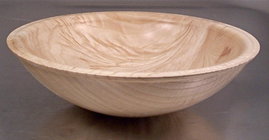
A platter like flat shape that has some twisting grain and knots will warp guaranteed, like this crotch feather grain and some knots as well, it became a wall hanging ;-)).
Here is another reason foe some warping, this is once turned Apple wood, where the center part is dark hearth wood and a wide area of sapwood, the sapwood is shrinking while the long grain heart wood is not, and so the sapwood side pulls the bowl into the shape you see.
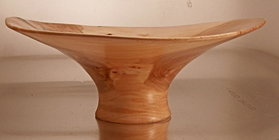
This Elm wood bowl is twisted for the warped grain that shrunk and twisted this bowl, were with straight grain this would not happen like this.
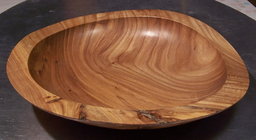
And then there is the wood that will twist and warp badly for where the wood came from, first off this is from wild Canada Plum and it's prone to warp, on top of that this came from the top of the root burl, mostly underground but for a small part, it really did a job on itself as you can see.
A thicker wall does not help with keeping the wood stable more likely the opposite, a 10% wall thickness for twice turned is plenty for all woods I know of, slow drying in a paper bag (nothing like curls or sawdust added !!) will give the wood to dry best also no sealer on the bowl if bag drying,
That is my experience and I have lots of that
