I'm now thinking about finish. As I've said, this piece is "rustic" (holes, cracks, piths, knots). So I don't want anything that clashes with that - so no built-up lacquer buffed to a high gloss or anything approaching that. I want it to still look and feel like wood.
I usually really like walnut oil on ash. It does yellow it a bit, but the color is warm and pleasing to me.
But I'm thinking I want something a tiny bit more "structural". OK, so no finish (short of epoxy or CA) is going to deal with the cracks, but I'd like something that might hold onto the frass I left behind. At least something that'll do a bit more than oil.
So I went with Osmo Poly-X Natural. It's easy to apply and should be tough (it's a finish for wood floors). And it doesn't really change the look of the wood much at all.
An aside about finishing hollow forms:
A finishing challenge is the inside.
Solvent-based finishes like lacquer or shellac can be poured in, rolled around, and wiped off (assuming you can get your finger etc in to wipe up the excess). But then you have to do something about the odor - I usually hook up a fish tank air pump and let it circulate air around inside for a few days. Even then it may still smell.
Things like walnut oil (and friends) can also be poured in and wiped off (again assuming you can). And the aroma is not such a problem (I still may fish-pump it unless I wiped it really good).
Any finish you pour on a piece like this one... well, it will come out all the holes and you get a real mess.
Osmo is thicker (doesn't run) and takes a tiny amount (so nothing to run even if it would) - and it's easy wipe-on, wipe-off.
Back to this one... I wiped Osmo inside the hollow form as best I could -made a brush from a folded bit of paper towel in some forceps. And did some with a paper towel wrapped around my finger. Didn't get the whole inside, but got what I could. Another wipe with a clean towel to remove excess.
Next, wiped the outside with Osmo on a paper towel. The bug holes really ripped up the towel, had to change a few times.
Next, I used a small brush to get finish in the worm holes.
Blew out excess with compressed air, then wiped the excess off the surface.
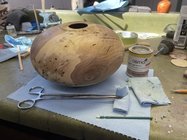
I'll do another coat later today... then get some photos to close this out.