Hello. New to woodturning. I'm a youth baseball coach, and many of our players use wood bats to train in the offseason. There's also a wood bat tournament that my team plays in. So my only interest is in making wood bats. Saw a couple videos on youtube, thought it looked cool, so I bought the cheapest lathe I could find, rigged it up on an old table saw, bought a few blanks, and got to work.
The lathe itself is one of those Vevor 14x40" models you can buy for $200.00. Came with a skew, a chisel, and a parting tool. So la-dee-dah, juust about everything about it was a complete pain in my *** to start. Here's an overview of the problems:
--- Mounted the lathe on the saw table with lag bolts, washers, and wingnuts, through a 1" thick x 3 foot flat piece of lumber (actually an old stair riser) to give it extra stability. Shaking is minimal as long as wood is properly balanced (big if)
---The tool rest was too low, and the allen wrench adjustment wouldn't hold it at the higher setting. The manual horizontal slider adjustment tightening bar conflicted with the junction where the lathe extension attaches (i.e. i couldn't slide the tool rest right or left toward the middle because the twist adjustment would jam up against the connection area). So ditched the bar, and got a wingnut for the bottom.
--- Also mounted the tool rest directly on the horizontal frame bar to get it 2-3" higher, and used some pieces of 2x4 as a shim on the other side to level it. Closer to the wood now, which made is usable for bat blanks.
--- Had a heck of a time manually adjusting the belt drive, which is the only way to change the speed/torque. But figured it out after much trial and error.
--- The spindle end tightener wheel slowly loosens when you turn the lathe on. So I ended up putting a nut on the threaded bolt that holds the pointy spinner thing, which more or less took care of that.
--- The spikey nut thing that holds the bat on the drive end needed to pounded into the center of the blank (or so the videos said). Well, that was a bunch of crap. But you do need to make like four precise 2mm holes on the blank for the 4 teeth on the spike nut. Then tighten the hell out of the other end to hold it secure.
--- The first few days, I had an issue with blank (37" ash or maple) shaking and popping off the lathe, so I got one of those steady rest things with the 3 plastic wheels. Then that popped off (plus the adjustment/tightening bars on that thing conflicted with parts of the lathe, and with itself!). So it ditched that piece of crap. The key was getting a good center finder for the ends of the blank, and tightening the spindle end so that sucker wouldn't pop off. Also, turning off the lathe (which is key) and tapping the spindle end base with a rubber mallet if it looked like it was not well aligned with the drive end (I'm dealing with like 37", so getting it right involves some ingenuity)
--- After my wife complained that the sanding process left a layer of dust on everything in the garage, most notably car, I rigged up a dust vacuum with an old shop vac, some flexible downspout tubing, and a cardboard 3D trapezoid suction. Cost roughly $10.00. Works surprising well.
So after much trial and error, and maybe another $100.00 wasted on modifications, here's my rig (with my 3rd bat on the hopper):
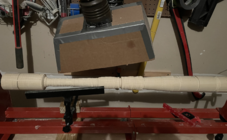
I'm sure everyone on here probably knows this already, but you basically divide the blank into 3 inch sections, use the parting tool to grind it down to the proper diameter (handle end is about 1.25", barrel end is ~2.25-2.5". Use a caliper to measure the diameter. Grind, measure, repeat (i can't measure while the lathe is on like some of those guys in the video, the calipers pop up off if they touch the bat). Then chisel the hell out of the areas in between, blend that sucker to make the transition between sections, get close to where you want to be, then go to work with the skew.
Here's my first one, with the two ends not sawed off. 34" about 38 ounces. Barrel on this was 2.75", so a lot of extra weight
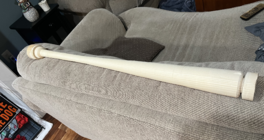
Bat #2, this one is maple, 33", 37 ounces with 2.75" barrel. Knob end not sawed down/finished in this pic. Again much larger than any kid should use (except for those dads that believe they have a superstar 11 year old because he's 5'2' 175lbs and can "swing with the big boys." but can't get around on a 60 mph fastball. My advice to those dads, lay off the nightly cheeseburgers and onion rings, that kid needs to play a position in the field if he want to even make it to High School, much less the Dodgers 2032 opening day roster):
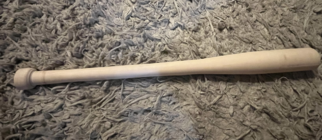
Bat #3, 33", 36 oz. Painted this one and Bat #2, what a mess that was. Still too big for an11-12 year old, but i'm working my way down there. Need to get one of those counter-sink drill bits to cup out the. You can see the nut on the spindle end that I rigged in the below pic
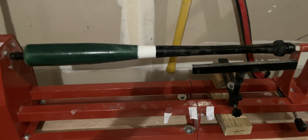
Skipping ahead to bats #4 and #5 (can't post any more pics because reached the 4 pic max). My wife bought me a new set of tools, which are really sharp (unlike the crap that came with the lathe). So took some getting used to. Made 2 more bats, both are about 32", and 35 and 33 ounces, 2.5" and 2 1/4" Barrels. Getting closer usable specs (for training only, way too heavy to use in a game).
Bottom line, this little $200.00 piece of crap lathe is doing its job after about 2 months, after some common sense modifications. Have not chopped off a finger, hand, or arm yet. Wear n95 masks during sanding process, so no COPD issues. Only interested in turning bats for now, so any tips are welcome, especially on a new tool rest that would be compatible with this thing because I need to be able to move it vertically (up and down, to the layperson) to get the new sharper tools to work properly as the diameter is reduced during the turning process. Look forward to posting more bats!
The lathe itself is one of those Vevor 14x40" models you can buy for $200.00. Came with a skew, a chisel, and a parting tool. So la-dee-dah, juust about everything about it was a complete pain in my *** to start. Here's an overview of the problems:
--- Mounted the lathe on the saw table with lag bolts, washers, and wingnuts, through a 1" thick x 3 foot flat piece of lumber (actually an old stair riser) to give it extra stability. Shaking is minimal as long as wood is properly balanced (big if)
---The tool rest was too low, and the allen wrench adjustment wouldn't hold it at the higher setting. The manual horizontal slider adjustment tightening bar conflicted with the junction where the lathe extension attaches (i.e. i couldn't slide the tool rest right or left toward the middle because the twist adjustment would jam up against the connection area). So ditched the bar, and got a wingnut for the bottom.
--- Also mounted the tool rest directly on the horizontal frame bar to get it 2-3" higher, and used some pieces of 2x4 as a shim on the other side to level it. Closer to the wood now, which made is usable for bat blanks.
--- Had a heck of a time manually adjusting the belt drive, which is the only way to change the speed/torque. But figured it out after much trial and error.
--- The spindle end tightener wheel slowly loosens when you turn the lathe on. So I ended up putting a nut on the threaded bolt that holds the pointy spinner thing, which more or less took care of that.
--- The spikey nut thing that holds the bat on the drive end needed to pounded into the center of the blank (or so the videos said). Well, that was a bunch of crap. But you do need to make like four precise 2mm holes on the blank for the 4 teeth on the spike nut. Then tighten the hell out of the other end to hold it secure.
--- The first few days, I had an issue with blank (37" ash or maple) shaking and popping off the lathe, so I got one of those steady rest things with the 3 plastic wheels. Then that popped off (plus the adjustment/tightening bars on that thing conflicted with parts of the lathe, and with itself!). So it ditched that piece of crap. The key was getting a good center finder for the ends of the blank, and tightening the spindle end so that sucker wouldn't pop off. Also, turning off the lathe (which is key) and tapping the spindle end base with a rubber mallet if it looked like it was not well aligned with the drive end (I'm dealing with like 37", so getting it right involves some ingenuity)
--- After my wife complained that the sanding process left a layer of dust on everything in the garage, most notably car, I rigged up a dust vacuum with an old shop vac, some flexible downspout tubing, and a cardboard 3D trapezoid suction. Cost roughly $10.00. Works surprising well.
So after much trial and error, and maybe another $100.00 wasted on modifications, here's my rig (with my 3rd bat on the hopper):
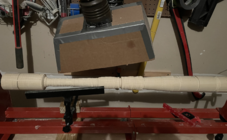
I'm sure everyone on here probably knows this already, but you basically divide the blank into 3 inch sections, use the parting tool to grind it down to the proper diameter (handle end is about 1.25", barrel end is ~2.25-2.5". Use a caliper to measure the diameter. Grind, measure, repeat (i can't measure while the lathe is on like some of those guys in the video, the calipers pop up off if they touch the bat). Then chisel the hell out of the areas in between, blend that sucker to make the transition between sections, get close to where you want to be, then go to work with the skew.
Here's my first one, with the two ends not sawed off. 34" about 38 ounces. Barrel on this was 2.75", so a lot of extra weight
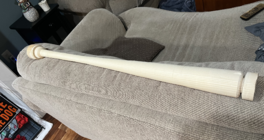
Bat #2, this one is maple, 33", 37 ounces with 2.75" barrel. Knob end not sawed down/finished in this pic. Again much larger than any kid should use (except for those dads that believe they have a superstar 11 year old because he's 5'2' 175lbs and can "swing with the big boys." but can't get around on a 60 mph fastball. My advice to those dads, lay off the nightly cheeseburgers and onion rings, that kid needs to play a position in the field if he want to even make it to High School, much less the Dodgers 2032 opening day roster):
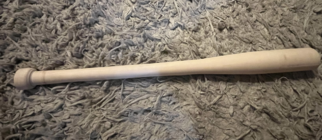
Bat #3, 33", 36 oz. Painted this one and Bat #2, what a mess that was. Still too big for an11-12 year old, but i'm working my way down there. Need to get one of those counter-sink drill bits to cup out the. You can see the nut on the spindle end that I rigged in the below pic
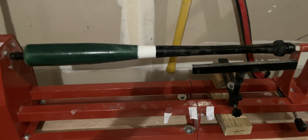
Skipping ahead to bats #4 and #5 (can't post any more pics because reached the 4 pic max). My wife bought me a new set of tools, which are really sharp (unlike the crap that came with the lathe). So took some getting used to. Made 2 more bats, both are about 32", and 35 and 33 ounces, 2.5" and 2 1/4" Barrels. Getting closer usable specs (for training only, way too heavy to use in a game).
Bottom line, this little $200.00 piece of crap lathe is doing its job after about 2 months, after some common sense modifications. Have not chopped off a finger, hand, or arm yet. Wear n95 masks during sanding process, so no COPD issues. Only interested in turning bats for now, so any tips are welcome, especially on a new tool rest that would be compatible with this thing because I need to be able to move it vertically (up and down, to the layperson) to get the new sharper tools to work properly as the diameter is reduced during the turning process. Look forward to posting more bats!
Last edited: