To get back on track. Thanks for all the suggestions, but my best option was to build my kiln to the dimensions I wanted. Note I have a secondary use for the kiln that is not drying wood for turning.
@Lou Jacobs Thanks for posting the ThermoPro sensor. I bought one after seeing your post and is ideal for this purpose IMO.
I had no idea what temperature I could reach, so I installed three light bases. Planned for worse case. My goals were 120F for drying turning wood and 135-140F for different use for the kiln. I got a small fan from the Restore to circulate air. Interior dimensions as 18” wide 38” long and 40” high. There are two removable shelves made from wire hardware cloth (I couldn’t find any wire racks that would fit). The first shelf is 16” above the lights and the second shelf is 12” above the first shelf. It is on wheels. With the doors closed I left a 3/8"” wide by 3/4" long gap to vent moisture. There is also some small gaps where the thermostat is installed.
Suggestions and comments are welcome.
Gap left in doors for venting about 3/8” wide and 3/4” long. There are also other openings.
Each light is controlled by a switch. I can turn on one, two or all three. They are all wired to the thermostat, if the temperature reaches the set point of 136F it will turn off all three. They turn back on at 135F. The fan is on a separate circuit and will run continuously. For drying turning stock I suspect I’ll only need one light. For my other use I’ll need two lights. Third light would be a spare if I noticed a bulb burnt out, not needed for temperature. Lights are 65 watt incandescent floods. The black cover is over the thermostat.
For testing, I got a small piece of wet walnut (24-27 MC) and turned a small bowl about 5” diameter and 3” tall and 5/8” -3/4” wall as a test piece. Weight was 450 grams (1 lb.) Sealed the end grain and put it in the kiln yesterday. I don t have good luck with walnut bag drying. I’ll see how this works. I’ll take a look and weight tomorrow. Just guessing it will be dry in 4 days because it is small.
This is a screen shot of the data from the sensor. Overnight the temperature remained fairly constant at 126F. You can see a rise this afternoon to 130F as the outside temperature is 97F. I suspect the kiln temperature will drop as it cools off overnight. Humidity is also slightly rising as it gets hotter outside.
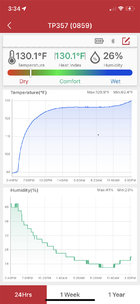