Idea for a hollowing system.
First turn the outside of your hollow form. Use a flexible spline to copy the outside curve on to paper. Offset that curve by the desired wall thickness. Your tool would have a cutter on one end and a pin protruding down to follow the tracer template. For example, maybe your tool shank is ten inches from cutter to pin. Draw a 10 inch line from points on inside curve of the hollow form through the pivot point. The location of the tracer pin establishes a point on the tracer template. Continue with a series of points inside your form to get a series of points to draw the template curve through those points. Cut the tracer curve template out of thin wood or whatever.
Once everything is mounted on your lathe with a drilled starting hole in your piece begin hollowing with your tool. The hollowing is complete when the pin is held tightly against the template contour to give the exact interior contour.
At least that's the theory. Comments? There'll be some details to be worked out about the location of the fixed pivot, etc.
It might seem that laying out the template contour would take quite a bit of time. Might not be as long a time as setting up conventional hollowing systems. This could be less expensive than other systems.
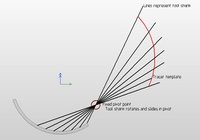
First turn the outside of your hollow form. Use a flexible spline to copy the outside curve on to paper. Offset that curve by the desired wall thickness. Your tool would have a cutter on one end and a pin protruding down to follow the tracer template. For example, maybe your tool shank is ten inches from cutter to pin. Draw a 10 inch line from points on inside curve of the hollow form through the pivot point. The location of the tracer pin establishes a point on the tracer template. Continue with a series of points inside your form to get a series of points to draw the template curve through those points. Cut the tracer curve template out of thin wood or whatever.
Once everything is mounted on your lathe with a drilled starting hole in your piece begin hollowing with your tool. The hollowing is complete when the pin is held tightly against the template contour to give the exact interior contour.
At least that's the theory. Comments? There'll be some details to be worked out about the location of the fixed pivot, etc.
It might seem that laying out the template contour would take quite a bit of time. Might not be as long a time as setting up conventional hollowing systems. This could be less expensive than other systems.
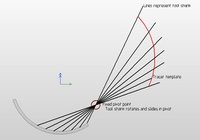