A few years ago I bought an articulated arm hollowing rig. While using it for that particular hollow form project I was struck by how versatile it could be for other aspects of turning. For tools that are held level such as NRS and carbide scrapers (or even Hunter style carbide tools) the rig holds the tool with pitch and roll fixed, so the orientation is always optimum. (Obviously we’re not talking about gouges and skews here). I found that I could use the rig to form the outside of a piece just as easily as the inside. And since the rig holds the tool a death grip is not required, just finger tip control, and you can leave the body motion for Latin dance class (where I got a failing grade).
It further occurs to me that an articulated arm rig could provide valuable assistance for a turner who is seated or has upper extremity limitations.
The rig I bought is called the Simple Hollowing System (SHS) and is made by Harrison Specialties. The SHS is pictured below mounted to the lathe bed in the usual fashion.
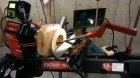
Other bed mounted articulated arm rigs might be used in a similar fashion, but one of the features of the SHS that lends it to this application is that the “arm and forearm” segments are long, while the “hand” segment is short. Note that the tool is already “long” so having a short hand segment is a benefit.
Even with a rotating headstock access to all the surfaces of the work was sometimes limited. So I made a standoff arm to add to the versatility of the rig. The design was a first guess prototype based on lthe try it and see if it works engineering school. It is made from scrap wood. It ended up working well enough that I never made a more refined version. Although there are a few things I would do differently if making another.
The pictures show most of the story.
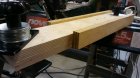
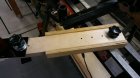
There are two pieces of ¾” plywood measuring 20” x 3 ¼” glued together to form the arm. To this I glued two 14 3/4” x 1 ¼” flanges of plywood sort of like an I-beam. The bottom is flat so it rests flat on the lathe bed. The back end is held down on the lathe bed using a steel plate under the ways and a threaded rod passing through the standoff to a knob. Similarly the hollowing rig is held down at the front end and can swivel to allow different positions. The threaded rods are longer than needed so that I can use the standoff and rig on other lathes. I have a stack of fender washers I use when the rods are too long. Notice that the side flanges must be shorter than the arm to allow clearance to swivel the base of the hollowing rig.
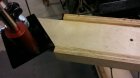
This construction turns out to be quite stiff. Whatever vibration theoretically exists it is not noticeable in actual use.
Things I would do differently:
The distance from the back end of the standoff to the hole for the plate and threaded rod is a little on the short side. Although the attachment is still rock solid I would increase this distance by an inch.
I would make the whole arm longer, probably 24” overall. It can always be cut down or the mounting holes moved if it’s too long, but usually I’m wishing I had just a little more standoff. Best thing to do if you want to make one for your lathe is clamp one end of a 2x4 to your bed and the other to the hollowing rig and try out different dimensions (motor off). I drilled extra holes, but they’re not necessary.
I have several pictures showing the positions available tool access that is available. Please note these are only mock-ups meant to show the range of motion possible. I didn’t even include a tool rest in some of the pics and I certainly would not be turning any of this wood as configured.
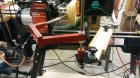
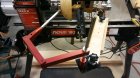
It further occurs to me that an articulated arm rig could provide valuable assistance for a turner who is seated or has upper extremity limitations.
The rig I bought is called the Simple Hollowing System (SHS) and is made by Harrison Specialties. The SHS is pictured below mounted to the lathe bed in the usual fashion.
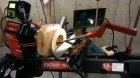
Other bed mounted articulated arm rigs might be used in a similar fashion, but one of the features of the SHS that lends it to this application is that the “arm and forearm” segments are long, while the “hand” segment is short. Note that the tool is already “long” so having a short hand segment is a benefit.
Even with a rotating headstock access to all the surfaces of the work was sometimes limited. So I made a standoff arm to add to the versatility of the rig. The design was a first guess prototype based on lthe try it and see if it works engineering school. It is made from scrap wood. It ended up working well enough that I never made a more refined version. Although there are a few things I would do differently if making another.
The pictures show most of the story.
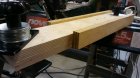
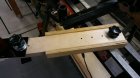
There are two pieces of ¾” plywood measuring 20” x 3 ¼” glued together to form the arm. To this I glued two 14 3/4” x 1 ¼” flanges of plywood sort of like an I-beam. The bottom is flat so it rests flat on the lathe bed. The back end is held down on the lathe bed using a steel plate under the ways and a threaded rod passing through the standoff to a knob. Similarly the hollowing rig is held down at the front end and can swivel to allow different positions. The threaded rods are longer than needed so that I can use the standoff and rig on other lathes. I have a stack of fender washers I use when the rods are too long. Notice that the side flanges must be shorter than the arm to allow clearance to swivel the base of the hollowing rig.
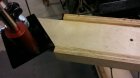
This construction turns out to be quite stiff. Whatever vibration theoretically exists it is not noticeable in actual use.
Things I would do differently:
The distance from the back end of the standoff to the hole for the plate and threaded rod is a little on the short side. Although the attachment is still rock solid I would increase this distance by an inch.
I would make the whole arm longer, probably 24” overall. It can always be cut down or the mounting holes moved if it’s too long, but usually I’m wishing I had just a little more standoff. Best thing to do if you want to make one for your lathe is clamp one end of a 2x4 to your bed and the other to the hollowing rig and try out different dimensions (motor off). I drilled extra holes, but they’re not necessary.
I have several pictures showing the positions available tool access that is available. Please note these are only mock-ups meant to show the range of motion possible. I didn’t even include a tool rest in some of the pics and I certainly would not be turning any of this wood as configured.
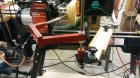
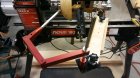
Last edited: