Bowl from a board (BFAB) tips
Many folks are very well aware of the BFAB way of making bowl blanks but some of us relatively new wood turners are not and might benefit from these notes. This way of making a bowl is actually fairly old. Previously it was primarily done on a scroll saw or a bandsaw but the rings can be cut from a board very effectively on a wood lathe.
I’ve only been doing BFABs for a couple weeks, after stumbling on some videos on YouTube describing the technique. I made a jig to hold the parting tool at 45, 50, 55, 60, 65, and 70 degrees from the face of the board from a piece of cherry and MDF and mounted it to my 12” tool rest with wood screws through the tool rest.
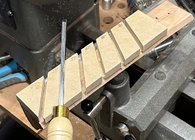
A couple things I’ve noted in watching videos and experimenting.
It helps to make a wooden cradle for over the lathe bed behind the board being cut so that when the ring separates from the board on the spindle it can’t get badly dinged up or broken on the bed of the lathe or the chuck.
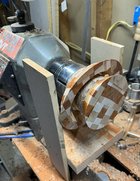
There’s no need to buy a thin parting tool. An extra standard parting tool can be modified on the slow speed grinder so the tip is narrower and more parallel with the surface of the board. This makes a cleaner cut when the parting tool cuts through the back of the board. I use the skew attachment on my Wolverine sharpening jig to grind the angle of the tip so its more parallel with the board surface, the cutting point is above the middle of the parting tool, and the bottom half of the shaft longitudinally is thinner than the top half. This greatly reduces and almost eliminates the chance of a standard parting tool binding up in the cut.
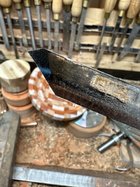
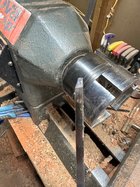
Many folks are very well aware of the BFAB way of making bowl blanks but some of us relatively new wood turners are not and might benefit from these notes. This way of making a bowl is actually fairly old. Previously it was primarily done on a scroll saw or a bandsaw but the rings can be cut from a board very effectively on a wood lathe.
I’ve only been doing BFABs for a couple weeks, after stumbling on some videos on YouTube describing the technique. I made a jig to hold the parting tool at 45, 50, 55, 60, 65, and 70 degrees from the face of the board from a piece of cherry and MDF and mounted it to my 12” tool rest with wood screws through the tool rest.
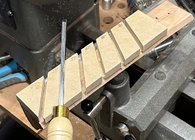
A couple things I’ve noted in watching videos and experimenting.
It helps to make a wooden cradle for over the lathe bed behind the board being cut so that when the ring separates from the board on the spindle it can’t get badly dinged up or broken on the bed of the lathe or the chuck.
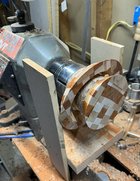
There’s no need to buy a thin parting tool. An extra standard parting tool can be modified on the slow speed grinder so the tip is narrower and more parallel with the surface of the board. This makes a cleaner cut when the parting tool cuts through the back of the board. I use the skew attachment on my Wolverine sharpening jig to grind the angle of the tip so its more parallel with the board surface, the cutting point is above the middle of the parting tool, and the bottom half of the shaft longitudinally is thinner than the top half. This greatly reduces and almost eliminates the chance of a standard parting tool binding up in the cut.
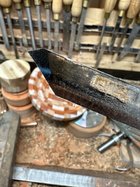
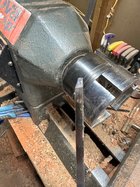
Last edited: