I saw the beautiful bowls that @Kent Reisdorph, and many other members, have posted and I was wondering what you are using to mark your bowls? The makers mark on Kent’s bowls really jumped out at me and I’m guessing that was done with a laser a that most are.
I’m at the hobbyist level and branding mine with a basic mark (below) but it’s a bit hit or miss with the application of the heat. I would like to move up to something better without breaking the bank so I am interested in what others are doing.
Thanks,
Bob
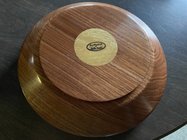
I’m at the hobbyist level and branding mine with a basic mark (below) but it’s a bit hit or miss with the application of the heat. I would like to move up to something better without breaking the bank so I am interested in what others are doing.
Thanks,
Bob
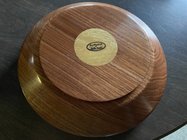