I'd love to hear your guys experiences with these two different kinds of systems and their different kinds of cutters.
24” c-c is long enough for an articulating system I think, but @Mark Jundanian would have a better idea.
Not entierly sure what I'm being asked to comment on, but here goes.
First a caveat or two. I do a lot of hollowing, but I don't make hollow forms like you're thinking of (
@GRJensen might have more direct experience using the SHS in that regard). Also I don't generally turn green wood, but rather as dry as I can find. This is a WIP, but an example of the kind of form I'm usually after:
So for me the contour is everything. If I have to start sanding at p60 or p80 I'm OK with that, indeed I use these "tools" to perfect the contour. So I want to say that without question carbide
scrapers leave a much rougher surface than do HSS gouges. That is just a price I am willing to pay (though I tell you, there are some days I would be willing to pay someone else to do it). What carbide scrapers bring to the table, particularly when used withe SHS, is the ability to create these contours. As to how carbide scrapers compare to HSS scrapers I can't really say.
For the sake of complete clarity let me say carbide like HSS is a material, not a tool per se, although we often use the term that way. Carbide is used to make cutters of various shape, square, round, diamond, etc. But more important is the different edge profiles. The most common is the scraper insert with a single bevel on the bottom and a flat top. Related are the new negative rake (top and bottom bevels) scraper inserts from EWT. And then there is another animal all together, the Hunter style cutters with a cupped or pie pan profile. These are not scrapers at all, but shear cutters.
The scrapers leave the roughest surface. The negative rake scrapers leave a much better surface, but you are still going to sand. The shear cutters can leave a very smooth surface. These require some skill to use correctly and I can't say that I have developed mastery. The shear cutters are also a very directionally sensitive tool. Where I will engage a round scraper or NRS anywhere from 8 to 12 and 12 to 4 O'clock, the shear cutters seem to work best between 11 and 1. So the two scrapers are the best tools for me use when creating contours. Where I have found the cupped cutters useful is in removing the bulk material. As I need start worrying a contour line I switch to a flat top scraper, and then when I'm in striking distance of the final contour line I switch to the more expensive NRS insert and a very light touch to get the least rough surface.
As GRJensen mentioned the SHS with the Simple Hollowing tool kit will work best at less than 9 inches depth (I would say 6 to 8). Indeed I think the tools only extend 9 1/2 inches out of the receiver. With the shapes I pursue I am able to introduce the tool rest deeper into the work piece than you would be able to with a narrow necked vessel, so I seldom have to reach farther than 6".
The SHS is sold with a 1/2" receiver, but if you're considering buying one I suggest purchasing the optional 5/8" reciever (and a set of Trent Bosch's reducers). You are not limited to using the Simple Hollowing tools with the SHS and the larger reciever creates some opportunities to use other tools. For example I have a Jackofsky hollower (with a cupped cutter) that I often use, as well as Thompson and D-way NR scrapers. You just have more options.
As far as tools for the SHS, EWT sells handleless versions of its tools, but these are only available directly from the company. If not the whole set, consider buying at least the 16 mm round tool as you can then get their NR inserts. The Simple Hollowing round tool mounts a 15 mm insert and so these are not interchangeable. The EWT tools are an inch shorter than the SH, though.
I don't think the SHS is the ideal solution for every hollowing task. If you're looking to hollow out an 18" vase, the SHS might work, but wouldn't be the best choice. But bed length can be another limitation. With the 15 24 laguna 12 inches might be the max. Figure 12 inches for the form plus 2 inches of waste wood and 4 inches for the chuck and you're already at 18 inches and looking for a place to mount the hollowing rig and the banjo. But I do encourage people to look at articulated arm systems when considering a hollowing rig (and I would definetly look at the new Elbow that Gerald Lawrence mentioned), because they are capable and very versatile. In fact for the peice pictured above I did the entire thing, top bottom, inside outside, all with the SHS. And we haven't even touched on how I've used it for other non-hollowing tasks.
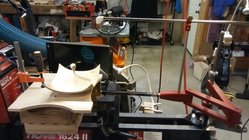
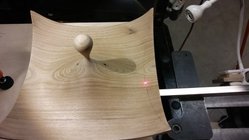
(The tool reads the template and the laser drops a dot. Mark with a pencil and the contour line is transfered).