Are there any recommendations for how deep a particular tool can safely go? ...
I think the depth depends on the wood, the particular tool (and sharpness), the length of the handle, and the experience and skill (and maybe a tiny bit the strength) of the turner. Pushing things can be dangerous!
This is a bit sideways from the original question, but have you looked at a "captive" hollowing system like the Jamiesson?
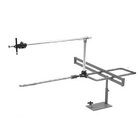
I have this and it is allows more depth than most hand-held tools. The design of the system restrains the tool from twisting.
Mine has been converted to replace the laser with a camera - using an overlay on a monitor lets you easily see the wall thickness all the way down the sides. Works with small hollowing projects too. Makes life easier. There are several companies that make similar systems, but they are not cheap. But if handy at metal working, you can easily make a similar system for cheap.
Did you ever see David Marks' big hollowing project? Amazing!
He used a similar constraint/captive system.
If you've never met David, he's a fantastic, kind, patient, and creative person. I still have a burled blank from him.
JKJ