Hi Mick,
I'm unfamiliar with rice bran oil as a bowl finish. Does it polymerize? Are there particular kinds of pieces you like using it on? Lovely little bowl, by the way. Thanks!
I inadvertently replied via message to Sarah, thinking I was replying in this thread. I clicked on the wrong thing in the email notification, again. This was my message to Sarah.
Sarah, thank you for your kind words with regard to my bowl.
As for Rice Bran Oil (RBO), well there was a shortage of Boiled Linseed Oil (BLO) during last winter for whatever reason, and as a result the price of BLO went through the roof, so I looked around and happened to see one of Richard Raffan's videos where he was using RBO, which was something I hadn't thought of. So I gave it a go as the cost for a 500ml bottle from Aldi was so cheap I had nothing to lose, and if things weren't good it could be used for cooking.
It has been a success, not a total success, but for timber that can handle the slight darkening, which usually brings out features on/in the timber, it is my go to oil these days. To answer your specific question about polymerising, I don't really know. This summer I've probably finished around 3 bowls a week, with around 4 out of 5 of those bowls finished with RBO, or another way, 80% have been finished with RBO.
Hopefully I've attached a few images, one is a finished bowl, which is Huon Pine, it is 120mm across and you may be able to see the growth rings; there are approximately 10 growth rings for every 10mm, which means that this section of tree shows 120 years of growth rings. Huon Pine comes from the Huon Valley in Tasmania and is irreplaceable as trees take around 1,000 years to reach maturity, their life span is estimated at 1,000 to 3,000 years. The wood has its own oil and it is a waterproof wood, and was used extensively for sailing ships. It is a protected species and all timber these days is retrieved from the bottom of rivers, where some of it is believed to have lain underwater for a couple of thousand years.
Consequentially, I've never purchased any Huon Pine, but I was lucky enough to be donated the offcuts of a fellow woodturner who purchased an approximately 450mm x 450mm by 190mm high piece of Huon Pine to make a largeish (for Huon Pine) bowl. My bowl shown below, is made from one of the three offcuts that were usable. One picture is of one of the offcuts and the finished bowl, which should show the difference in colour obtained on this timber with RBO.
Huon Pine, I found out, cannot be finely sanded, the sandpaper just oils up. I started at 120 grit, then progressed through the grits until 180 grit. Once I applied 240 grit, the sandpaper basically just oiled up. Regardless, this first of three bowls is wonderfully smooth and feels as though 600 grit has been used. One is always learning!
A link to Huon Pine, which I've just found out, is not a pine after all!!!!
en.wikipedia.org
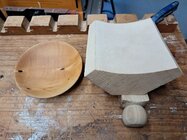
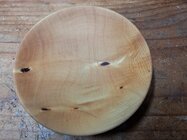
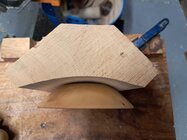