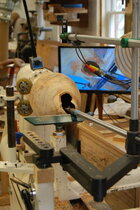
I was having a heck of a time hollowing this spalted maple vase, 8" d. x 12"h. using a 3/4" Jamieson boring bar in a Bosch Stabilizer. The workpiece is heavily spalted on one face and sound on the other, alternately dense and soft, and unbalanced- I could spin it at only about 450 rpm without shuddering and the tool was bouncing badly even with a slow feed rate. I got about 2/3 of the way in and was seriously wondering if I would be able to complete the piece at all. I decided to try a setup I had used in the past to extend the reach of the boring bar by using a separate tool rest in a second banjo, which did the trick.
I really like the Bosch hollowing jig for its compact size and easy setup, but it turns out that combining the tool rest and the boring bar mount on a single 1" post is not as resistant to leverage and vibration as the alternative shown here. If you have a spare banjo this can extend the limits of the Bosch rig.
Last edited: