Alright I just finished up two more bowls and cut them in half for some more C&C
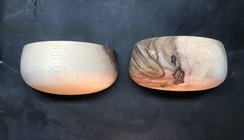
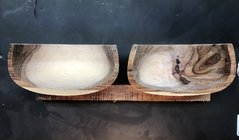
I checked more often with my calipers and I checked my depth multiple times as I neared the bottom, I use the chuck key sighted across the rim to check my depth but the gauge is a good idea. I made a point to leave the bottom a little thicker and that worked out well in my eyes at least. I don't have a carbide, so I did use a scraper a little bit on the bottom of the bowl at right to clean it up a little bit which helped in the corners a bit. I did taper the sides a tad to see how that would go with the thicker bottom.
@Emiliano Achaval I did the the thickest part 1/3 of the way up instead of 2/3, which is what I did on the original ones. I was pleasantly surprised how nice these felt and the fact that they weren't any more difficult to turn then the original ones. Are these more traditionaly accurate? I also did some looking and found a used copy of Irving Jenkins book for a good price and went ahead and ordered it and look forward to reading it.
@robo hippy , the bowls I am cutting in half are the ones with major cracks, from poor blank lay out on the log, so they are fire wood anyways and if I can learn from firewood then I am happy.
The calipers I have been using are the small jackovsky calipers but I will try out the wire calipers on the next batch and see how they do.
I have seen your videos on the armrest and on the depth gauge and I think they are brilliant. My only problem is for the gauge, I would need several for each chuck and some of the longer jaws that I have.
I sand these while they are green and find that works well for the ones I have been doing. I really like your armrest I just haven't taken the time or discovered my dire need to make one just yet.
Thanks again to you all for the help and please continue to give your thoughts on these bowls and what I can do better next time. I really appreciate this and it really is already making a difference.