Hi there. I've just joined the group, and am a novice woodturner, living in E TN near Knoxville. I inherited my Dad's lathe, a late 20th century model Woodfast M408. Though my Dad had shown me how to do basic turning years ago, and I've more recently (past 5 years) taken a couple classes, elder-care issues have prevented me from EVER making the time to get on the lathe. Thus, my lathe has been dormant 5+ years, and I've never taken it up.
That said, a gentleman in our local community woodworking group has graciously given me 2 lessons this past week, and I completed my first vessel (see first photo). I'm really happy with it (despite the Long Hours of reaming it out
! Unfortunately, though, in the midst of the work this week, my tailstock somehow locked up and I believe is totally fried now. Either the threads of the guide wheel got cross-threaded, or other internal parts malfunctioned. And, unfortunately, this model is no longer made and the manufacturer has no spare tailstock or parts. I HATE that I'm now hamstrung prior to really getting my feet wet, as I'm totally out of operation until I figure out how to proceed.
Being brand new to this organization, I'm likely posting the following in the wrong forum, so I'll beg forgiveness now...and proceed. Does anyone in the club have advice as to where I can find an OEM tailstock? Or, a comparable tailstock (mine is 8-1/4")? Other fix?
Thanks.
Chris Bahn
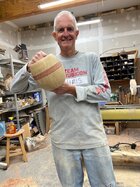
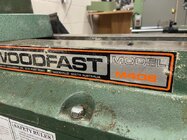
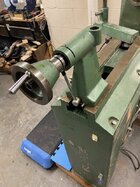
That said, a gentleman in our local community woodworking group has graciously given me 2 lessons this past week, and I completed my first vessel (see first photo). I'm really happy with it (despite the Long Hours of reaming it out

Being brand new to this organization, I'm likely posting the following in the wrong forum, so I'll beg forgiveness now...and proceed. Does anyone in the club have advice as to where I can find an OEM tailstock? Or, a comparable tailstock (mine is 8-1/4")? Other fix?
Thanks.
Chris Bahn
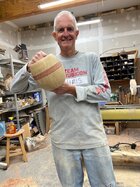
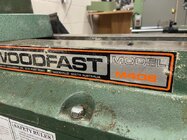
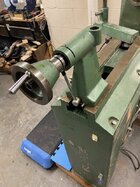