I have this stainless steel enclosure with glass back and glass door. It's about 20 x 16 x 20 deep. A scientific drying rack, I'm guessing was its originally use. No holes in it. Has 2 mesh shelves and one solid one. Plan to modify it for a dryer. Will probably hold 6 large bowls at a time. Likely pretty air tight. Those who have done it, any advice you could lend to how best to heat would be appreciated.
Should I insulate it?
Best spot for bulb?
Bulb type/wattage to use?
Fan needed? Vented or just circulate? Placement relative to bulb?
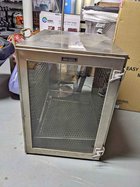
Should I insulate it?
Best spot for bulb?
Bulb type/wattage to use?
Fan needed? Vented or just circulate? Placement relative to bulb?
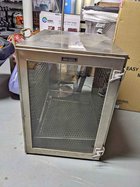