Ha! LOVE the pencil holder! I could put those every 5' around my little shop and still not be able to find one when I need one.
Amen! Imagine working at the lathe without a pencil!
Since I like my lathe against the wall, in addition to a cup for various pencils on the small shelf, I use a different method to keep them at hand - magnets. Use them for small, often reached-for tools too, measuring tapes, rulers...
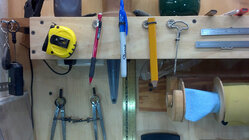
Some pencils, especially mechanical pencils with steel clips, will stick to a magnet. For others, I wrap a couple of turns of soft iron "bailing" wire.
When a Sharpie runs low on ink, I simply pull off the little circle of wire and slide it on a fresh Sharpie.
BTW, the I added the vertical plywood facing on the small shelf for two reasons: one, to hide the outlets and wires for lights, second, for a place to hold magnets! I use the type of magnets that are made to be held with a wood screw. For a heavy item, stronger magnets are available held by two small wood screws.
On the lathe itself, magnets without screws work. If a magnet is strong enough to hold what I want but weak enough to slide around a bit, I've been known to use a dab of epoxy.
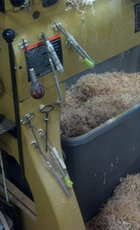
I use magnets for a variety of other tools at the lathe - awls, screw drivers, hex keys, center punches, gimlets, etc.
And at the bandsaw:
Another use for a magnet: keep a shiny one mounted somewhere in your shop. If using a CBN wheel, note how it will collect extremely fine black steel dust that floats through the air. Unless breathing fine steel dust is good for the lungs, it's a reminder to use a respirator for sharpening too.
The dust floats all around the shop - I've found magnets on the bandsaw covered with steel dust, 10' away on the side facing away from the grinders. With the room lights turned off and a single bright directed light it's easy to see fine steel particles floating through the air.
JKJ