odie
TOTW Team
- Joined
- Dec 22, 2006
- Messages
- 7,117
- Likes
- 9,858
I feel it's not good manners to critique other's turnings, unless they specifically ask for it. I realized after offering some freebie roughed bowls in the "for sale" section, that this would give me a good opportunity to tell newbie turners what to look for in their own roughed bowls.....by self-evaluating my own roughed bowls.
Even in the roughing stage, it's to your best advantage to have as little tearout as possible.....because tearout disrupts wood fibers beneath the surface. In the second turn, if your initial roughed bowls have an excessive amount of tearout, it could, and often does effect how well of a cut is possible in any later stage of the turning. Any tearout needs to be removed completely, which includes any disrupted wood fibers below the surface. This doesn't mean you can sand your way to a good surface......because any disrupted fibers left after sanding will show up in what otherwise looked like an acceptable surface prior to sanding.....at that point, your eyes are deceiving you! Most often, these disrupted fibers will show up in the form of a seemingly blurred wood grain, and not a crisp cleanly revealed wood grain. This condition is not easily recognized by the new turner with an untrained eye, but is more apparent to those who understand what they are looking for.
OK......now here are some of my roughed bowls. They were roughed in the usual manner I normally do, so they weren't done for the purposes of display to make a point. You can inspect these roughed bowls by clicking twice for a closer look. Certainly, they aren't devoid of tearout, but there is a minimum of it here......most noticeably in the bottom left and right bowls. This is generally what you want to see in your roughing work. (Zero tearout would be better!) We've all seen roughed bowls in these forums with lots of tearout.....that is exactly what you don't want.
During the roughing stage, it is my practice to bring a bowl to round with scrapers, and then seek a more refined surface with gouges. (I understand others may rough differently than I do, and we'll probably hear from them in this thread. The point being made here, is to end up with a surface with as little tearout in the roughing stage as possible.) If there is a lot of tearout after the roughing stage is done, then you need to evaluate your technique, tool choice, and the level of sharpness you are working with.
-----odie-----
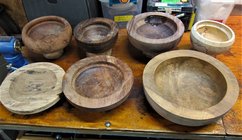
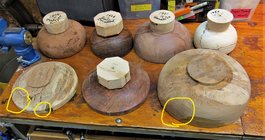
Even in the roughing stage, it's to your best advantage to have as little tearout as possible.....because tearout disrupts wood fibers beneath the surface. In the second turn, if your initial roughed bowls have an excessive amount of tearout, it could, and often does effect how well of a cut is possible in any later stage of the turning. Any tearout needs to be removed completely, which includes any disrupted wood fibers below the surface. This doesn't mean you can sand your way to a good surface......because any disrupted fibers left after sanding will show up in what otherwise looked like an acceptable surface prior to sanding.....at that point, your eyes are deceiving you! Most often, these disrupted fibers will show up in the form of a seemingly blurred wood grain, and not a crisp cleanly revealed wood grain. This condition is not easily recognized by the new turner with an untrained eye, but is more apparent to those who understand what they are looking for.
OK......now here are some of my roughed bowls. They were roughed in the usual manner I normally do, so they weren't done for the purposes of display to make a point. You can inspect these roughed bowls by clicking twice for a closer look. Certainly, they aren't devoid of tearout, but there is a minimum of it here......most noticeably in the bottom left and right bowls. This is generally what you want to see in your roughing work. (Zero tearout would be better!) We've all seen roughed bowls in these forums with lots of tearout.....that is exactly what you don't want.
During the roughing stage, it is my practice to bring a bowl to round with scrapers, and then seek a more refined surface with gouges. (I understand others may rough differently than I do, and we'll probably hear from them in this thread. The point being made here, is to end up with a surface with as little tearout in the roughing stage as possible.) If there is a lot of tearout after the roughing stage is done, then you need to evaluate your technique, tool choice, and the level of sharpness you are working with.
-----odie-----
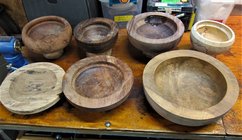
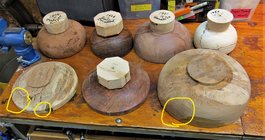