When I mentioned needing faceplates with a 33mm thread my friend and mentor Tom Dunne offered me several and asked me if I could get two others tuned up in return. I received a 4" Oneway, a welded 6" and this massive 10" faceplate with adjustable counterweights and a 33mm spindle boss for chuck mounting. I will add screw holes around the circumference to make it more versatile. Is this design familiar to anyone? Tom does not recall where he got it.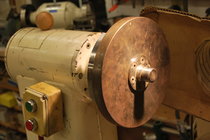
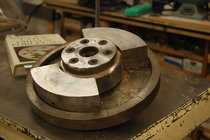
I took away two Oneway faceplates that needed attention. The first, a 6", showed .038" runout measured at the rim face. I couldn't reach the machinist I wanted to look at it and decided to true it up by hand, which turned out to be quite tedious but doable with patience and a hss scraper. The other, at 10", is cracked next to the tapered insert screws and is also showing .040" runout. My general feeling is that it should be scrapped, but perhaps it can be welded or brazed and flattened. I am afraid repairing it may be less than 100% reliable, which is not what is wanted when you need a 10" faceplate. I do know several skilled metal fabricators. What say you all?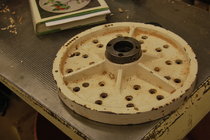
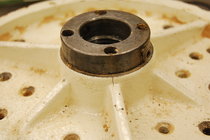
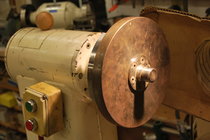
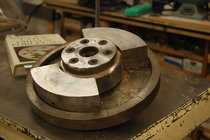
I took away two Oneway faceplates that needed attention. The first, a 6", showed .038" runout measured at the rim face. I couldn't reach the machinist I wanted to look at it and decided to true it up by hand, which turned out to be quite tedious but doable with patience and a hss scraper. The other, at 10", is cracked next to the tapered insert screws and is also showing .040" runout. My general feeling is that it should be scrapped, but perhaps it can be welded or brazed and flattened. I am afraid repairing it may be less than 100% reliable, which is not what is wanted when you need a 10" faceplate. I do know several skilled metal fabricators. What say you all?
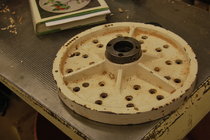
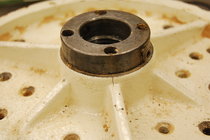