Whether it’s NIP or Cook pine doesn’t matter but ever since seeing a buying a Ron Kent bowl some 37 years ago, I’ve loved the wood. Though Ron has passed, his eponymous site has good info re wood stabilization and his technique. So as I’ve started turning, I’ve found a source and have made some pieces with it. I’ve been trying to figure out the knot structure and came across a good source not only for decent size blanks but also an explanation of the knot orientation so as to turn and get a star.
No affiliation, but this site has sizeable blanks: http://www.woodturningblanks4u.com/norfolk-island-pine-turning-wood.html
and led me to the understanding of anatomy of NIP:
I find it interesting that they recommend turning NIP end grain bowl interiors first, stopping when the desired internal pattern is reached, then turning the outside. Will take some thinking to do that.
Curious about the experience of others with this wood.
No affiliation, but this site has sizeable blanks: http://www.woodturningblanks4u.com/norfolk-island-pine-turning-wood.html
and led me to the understanding of anatomy of NIP:
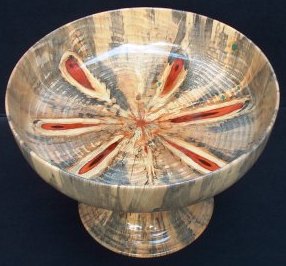
Norfolk Island Pine Tips
Norfolk Island Pine tips to improve your woodturning results.
www.woodturningblanks4u.com
I find it interesting that they recommend turning NIP end grain bowl interiors first, stopping when the desired internal pattern is reached, then turning the outside. Will take some thinking to do that.
Curious about the experience of others with this wood.