Thanks for all the 3rd party rest ideas. Funny, at Steve Sinner's site he has a note from Trent Bosch on how well he enjoys Sinner's tool rest. (Likely before Bosch started building his own.)
I just spent some time looking critically at the banjo and tool rest and how my hand naturally engages with them. When the rest is dropped at a typical, arbitrary, non-measured height below machine axis center, from top of banjo to top of rest, that height is 2" +/- a fraction. Here are a few pics, more of a mock-up (no wood on the machine). The rest is actually a bit higher in the pics but still below center. As I/we can see, along with my middle finger finding the post, my ring finger is grazing the top of the banjo.
It seems the method Oneway chose to clamp the rest, on the operator's side of the banjo vs. the common right side of the banjo, may result in the banjo being proportionally taller where the rest inserts vs. how other clamping designs may be arranged on other similar height lathes.
Rather than investing in different tool rests which may, in the end, not provide the clearance I initially inquired about (which turns out to be more clearance to the banjo that the rest post), I am going to try adjusting my hand grip with the tool, and an even more deliberate rest height out of the banjo (put some etch marks on the rest post like I've done with my Vicmarc lathe), and when called for utilize an overhand grip more often.
Now that I've looked closely and analyzed what I've experienced, I may be able to simply retrain nearly 30 years of muscle memory to make this what it likely is- a non-issue.
Thanks again for the ideas, I'll explore them more if necessary.
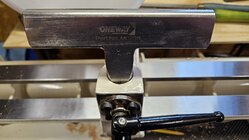