Norm I have turned Honey Locust quite a bit, but I always twice turn it, I do like the look of the grain and color of Honey Locust just take your time and the right way.
There are a few things you should know about Honey Locust wood, yes it is hard, aside of that, the sap wood shrinks more than the heart wood and it will split if you don't take care of preventing the wood from drying fast (DAMHIKT)
Also Honey Locust is a open grain wood, just as much or more than Red Oak, we have still one of my first Honey Locust bowls with an oil finish that would not dry and kept bleeding the oil, still is sticky now, seal the grain if you want to use an Oil finish and don't saturate the grain with oil, or add a second coat before the first one is dry.
So I suggest you dry it slowly in a brown paper bag and then use something that will seal the grain before adding a finish.
Sanding it is not a problem as the wood does not warp a lot, the bark stays on with every Honey Locust I have turned, with the bark still on you can power sand if you hold the bowl still (I block the lathe and sand that way.)
Here is my. last finished natural edge Honey Locust bowl
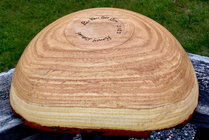