I haven’t turned for a long time but I always knew I’d get back to it and never stopped accumulating interesting pieces.
This piece has been sitting in my shop for about 15 years. I forget what species it is. I know it came from a big bush that I had taken out.
The vision has always been to turn a vase, leaving the top branch stubs to be carved into leaves. The hole in the bottom is a little over an inch deep but is solid hardwood below it, I’ll cut that section off.
My turning skills have to improve a lot before I would tackle this and I’ve never carved so I need to develop those leaf carving skills. I plan to join an AAW branch to hook up with a mentor that ca help guide me.
So, this is a project for the future but I’m curious. What do you guys think of the feasibility of this project, once I have the proper skills. Aside from breaking fingers from those branch stubs spinning around when hollowing, what issues do you see?
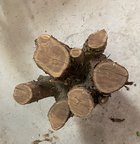
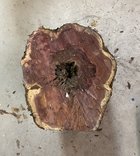
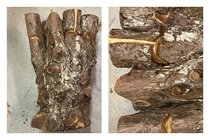
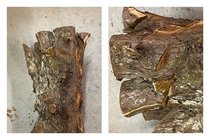
This piece has been sitting in my shop for about 15 years. I forget what species it is. I know it came from a big bush that I had taken out.
The vision has always been to turn a vase, leaving the top branch stubs to be carved into leaves. The hole in the bottom is a little over an inch deep but is solid hardwood below it, I’ll cut that section off.
My turning skills have to improve a lot before I would tackle this and I’ve never carved so I need to develop those leaf carving skills. I plan to join an AAW branch to hook up with a mentor that ca help guide me.
So, this is a project for the future but I’m curious. What do you guys think of the feasibility of this project, once I have the proper skills. Aside from breaking fingers from those branch stubs spinning around when hollowing, what issues do you see?
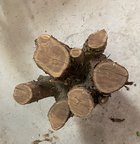
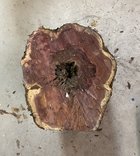
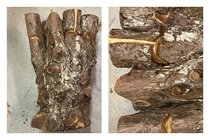
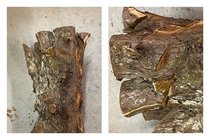
Last edited: