After using my Robust banjo for several years, I'm finding that the screw threads for the clamp blocks have stripped. The problem is this screw is not hardened like a normal bolt would be. The cause is my cranking on the handle too hard, and over time, the threads at the tip have bent over, and eventually failed. I have replaced this locking handle with a new one from McMaster Carr. The description and part# is as follows:
Zinc Adjustable-Position Handle
with 3/8"-16 Threaded 2-3/8" Long Stud, 2-5/8" Projection, Black
6271K71
If you haven't checked the threads on your locking handle, you should.....only takes a second to slide it out and look.
Photo shows my damaged threads on bottom, and the new replacement part.
-----odie-----
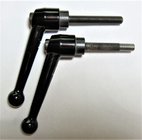
Zinc Adjustable-Position Handle
with 3/8"-16 Threaded 2-3/8" Long Stud, 2-5/8" Projection, Black
6271K71
If you haven't checked the threads on your locking handle, you should.....only takes a second to slide it out and look.
Photo shows my damaged threads on bottom, and the new replacement part.
-----odie-----
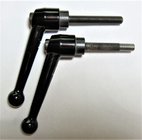
Last edited: