Hi folks,
Is it “safe” to make a bedan style lathe chisel out of a piece of 3/8” metal lathe tool steel?
I picked up multiple metal lathe cutting tools with an antique Barnes 4 1/2 velocipede (pedal powered) metal lathe I brought home last week to use as a foot powered wood lathe. It included a wooden box full of original Barnes accessories as well as metal lathe tools, both old ones as well as more modern appearing ones.
I inserted one of them into 1/2” square steel tube as it was too short otherwise. I intend to insert that into an ash handle I’m turning on the lathe to make a cheap version of a 3/8” bedan type chisel. I already roughed out this 2” square piece of ash with this makeshift bedan and it’s a real hogging machine, even without a handle. So it certainly seems effective.
I noticed as I was tapping the metal lathe tool into the 1/2” square steel tube with a hammer, the tip cracked off very easily, as if it was very hard but also fairly brittle. Probably a dumb mistake, I admit.
I subsequently ground a bedan type grind on it. I had previously modified an extra 1/4” thick parting tool into a bedan style grind and find it to be a very handy and effective tool.
I’m assuming that the brittle nature of the metal lathe tool steel won’t be a problem while using it as a bedan style lathe chisel?
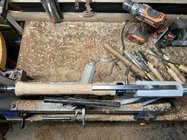
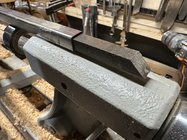
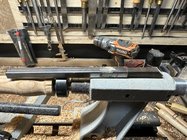
Is it “safe” to make a bedan style lathe chisel out of a piece of 3/8” metal lathe tool steel?
I picked up multiple metal lathe cutting tools with an antique Barnes 4 1/2 velocipede (pedal powered) metal lathe I brought home last week to use as a foot powered wood lathe. It included a wooden box full of original Barnes accessories as well as metal lathe tools, both old ones as well as more modern appearing ones.
I inserted one of them into 1/2” square steel tube as it was too short otherwise. I intend to insert that into an ash handle I’m turning on the lathe to make a cheap version of a 3/8” bedan type chisel. I already roughed out this 2” square piece of ash with this makeshift bedan and it’s a real hogging machine, even without a handle. So it certainly seems effective.
I noticed as I was tapping the metal lathe tool into the 1/2” square steel tube with a hammer, the tip cracked off very easily, as if it was very hard but also fairly brittle. Probably a dumb mistake, I admit.
I subsequently ground a bedan type grind on it. I had previously modified an extra 1/4” thick parting tool into a bedan style grind and find it to be a very handy and effective tool.
I’m assuming that the brittle nature of the metal lathe tool steel won’t be a problem while using it as a bedan style lathe chisel?
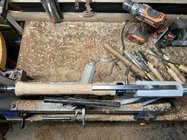
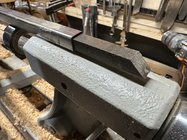
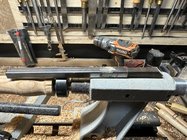
Last edited: