So one of the reasons I upgraded to the PM 3520C was so I could turn larger work. I just got this 14x3" kiln-dried cherry blank to make a shallow bowl/deep platter display piece for a co-worker. It will be the most massive thing I have had on the lathe yet-my biggest previously was an 11x5" maple bowl. Just the weight and heft of it have me questioning my current holding chucking methods, so please indulge a few questions:
Face-plate(s): I haven't done much on face-plates, but I thought I would start this one on a face-plate while I work on the tenon, outside/bottom. My PowerMatic faceplate that came with the lathe is just a little over 3 inches, and is dwarfed by the blank. I feel like I need a bigger one for this. Is there a size-ratio rule there? What's a good general face-plate for bigger stuff?
Chucking: I've got the RecordPower SC4 chuck, and I just ordered the 130mm jaws for bigger work. Is this big enough, or do I need even bigger jaws?
Speaking of chucking and jaws, the customer asked me to preserve as much depth as possible. What would be the minimum safe depth for the tenon? And would it be safe to put a piece this massive on a glue block? I would be afraid the torque would send it flying in the event of a catch (thankfully rare for me any more) or a quick stop.
For what it's worth, I'm taking David Ellsworth's 3-day class later this summer. I'm hoping I'll have a lot of fundamentals like this sorted out before then so that I can concentrate more on form, more advanced tool control and techniques. Anyway, thanks as always for any help! Aaron
By the way, order with confidence from https://www.turningblanks.net/ . They shipped this overnight along with a free maple spindle. I have driven down to their warehouse in Donalds, SC a few times to pick through their ample stock, and those guys always take care of me. It's just a nice, well-run family business.
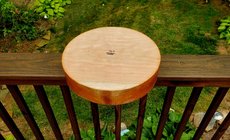
Face-plate(s): I haven't done much on face-plates, but I thought I would start this one on a face-plate while I work on the tenon, outside/bottom. My PowerMatic faceplate that came with the lathe is just a little over 3 inches, and is dwarfed by the blank. I feel like I need a bigger one for this. Is there a size-ratio rule there? What's a good general face-plate for bigger stuff?
Chucking: I've got the RecordPower SC4 chuck, and I just ordered the 130mm jaws for bigger work. Is this big enough, or do I need even bigger jaws?
Speaking of chucking and jaws, the customer asked me to preserve as much depth as possible. What would be the minimum safe depth for the tenon? And would it be safe to put a piece this massive on a glue block? I would be afraid the torque would send it flying in the event of a catch (thankfully rare for me any more) or a quick stop.
For what it's worth, I'm taking David Ellsworth's 3-day class later this summer. I'm hoping I'll have a lot of fundamentals like this sorted out before then so that I can concentrate more on form, more advanced tool control and techniques. Anyway, thanks as always for any help! Aaron
By the way, order with confidence from https://www.turningblanks.net/ . They shipped this overnight along with a free maple spindle. I have driven down to their warehouse in Donalds, SC a few times to pick through their ample stock, and those guys always take care of me. It's just a nice, well-run family business.
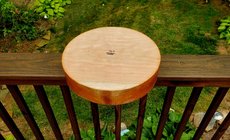