Well, OK, if we're going to drop our drawers, so to speak...
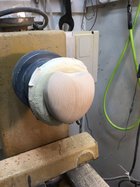
This is an alder heart that is my prototype (attached to my vacuum chuck, with the second face just sanded).
In the past, I would throw a nice chunk of wood on the lathe and assume I would be able to produce the desired new project the very first time. Wrong. One of the most valuable lessons I've learned in my turning journey is that doing a couple of practice pieces with a new project allows me to learn where the challenging parts will be, fill in any gaps in the instructions, and get my work flow down, which may be a little different than the originator of the project. THEN, mount the nice wood and make one.
Michael's heart instructions were spot on, easy to follow, and I didn't find any gaps. I did learn that it's critical to sand the 'bowl' at the top of the heart right after it's turned and still chucked up. It's surprisingly hard to hand sand end grain down in a little depression. Another lesson I learned is that it's helpful to make pencil marks indicating the central circumference, like when turning a bead, so the front and back of the heart are equal and have the same curve. This isn't a necessary quality, and others might like some asymmetry, but I wanted it equal. One modification I made was to allow a little extra wood at the end of the blank where the point will be to use for making a tenon to chuck.
I've been wanting to turn a heart for a very long time and Michael's instructions allowed me to do it. Thank you, Michael! Now where did I put the nice square 6" blanks???