I've wanted a vacuum chuck system for a long time, but was impeded because the spindle on my lathe did not have a through hole. Well, now it does! Yay.
And last week I was innocently perusing Kijiji, when I came across a refrigeration manufacturer that is blowing out their old vacuum pumps. I picked up an Edwards RV8 for, reconditioned, for $100, including hoses and an air oil separator.
(BTW - they have a few more skids of these. If anyone is interested, I'll point you there - no affiliation)
So, I read through carious posts and articles, and am making my showing list of missing parts.
Here's how I "think" it will go together. Please let me know if any improvements are suggested.
The pump will go in the attic, along with the filter(s) and will vent outside.
Air filter - It seems I can use a normal pneumatic air filter, with vacuum, instead of pressure.
Supplied hoses are all quick connect. So I might have Princess Auto make up the remaining, in similar fashion.
Bleed valve will likely be a 1/2" ball valve - I've seen posts where the valve was too small to lower the pressure sufficiently.
Air reservoir tank. Some designs, like Joe Woodworker, has a tank inline, so the pump does not need to run continuously. And I would have to add vacuum switch(es) to turn the pump on/off. Is that advisable? It would be a Phase 2 requirement.
I'm very open to suggestions about alternative solutions.
Thanks
And last week I was innocently perusing Kijiji, when I came across a refrigeration manufacturer that is blowing out their old vacuum pumps. I picked up an Edwards RV8 for, reconditioned, for $100, including hoses and an air oil separator.
(BTW - they have a few more skids of these. If anyone is interested, I'll point you there - no affiliation)
So, I read through carious posts and articles, and am making my showing list of missing parts.
Here's how I "think" it will go together. Please let me know if any improvements are suggested.
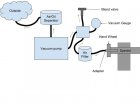
The pump will go in the attic, along with the filter(s) and will vent outside.
Air filter - It seems I can use a normal pneumatic air filter, with vacuum, instead of pressure.
Supplied hoses are all quick connect. So I might have Princess Auto make up the remaining, in similar fashion.
Bleed valve will likely be a 1/2" ball valve - I've seen posts where the valve was too small to lower the pressure sufficiently.
Air reservoir tank. Some designs, like Joe Woodworker, has a tank inline, so the pump does not need to run continuously. And I would have to add vacuum switch(es) to turn the pump on/off. Is that advisable? It would be a Phase 2 requirement.
I'm very open to suggestions about alternative solutions.
Thanks