Hi,
I acquired a secondhand vacuum pump and bag press a few months ago and have only just got round to sorting the rest of the system. Pleasantly surprised by how well it works so I thought I'd share my experiences.
I turned an aluminium shaft, on the wood lathe with three little coves to fit three O rings that were a snug fit within the spindle, (Spindle bore approx. 16mm on my 3520B) much trial and error required to get the sizing right, and a little Vaseline for lube helps. Used a mixture of HSS cutters, sharpened as they would be for use in a metal lathe, as well as a standard skew and spindle gouge. Another O ring also sits tight up against the handwheel (I feel the more the merrier) and a hole bored through the middle, drilled out in the usual way with a Jacobs chuck in the tailstock. Sealed bearings are required and I used a couple that I had in stock.
Once again using what I had available, an old Nylon (some sort of plastic) material roller (another thing that I knew there was a reason for keeping) was hollowed out to fit the outside of the bearings. The inner part of the nylon was drilled out and the hose barb was screwed in.
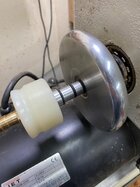
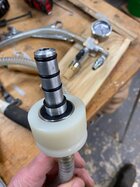
Fittings, gauge and valve purchased and fitted together with PTFE tape and off we go. Used a sintered exhaust silencer as a filter below the quarter turn valve and then this was attached to the lathe using one of the belt cover bolts, which makes it easily removable.
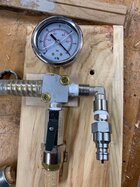
Very poorly produced video making the adapter (and you'll be able to find others on the manifold and chuck)
Adapter Video
More chucks to make. further details to follow.
I acquired a secondhand vacuum pump and bag press a few months ago and have only just got round to sorting the rest of the system. Pleasantly surprised by how well it works so I thought I'd share my experiences.
I turned an aluminium shaft, on the wood lathe with three little coves to fit three O rings that were a snug fit within the spindle, (Spindle bore approx. 16mm on my 3520B) much trial and error required to get the sizing right, and a little Vaseline for lube helps. Used a mixture of HSS cutters, sharpened as they would be for use in a metal lathe, as well as a standard skew and spindle gouge. Another O ring also sits tight up against the handwheel (I feel the more the merrier) and a hole bored through the middle, drilled out in the usual way with a Jacobs chuck in the tailstock. Sealed bearings are required and I used a couple that I had in stock.
Once again using what I had available, an old Nylon (some sort of plastic) material roller (another thing that I knew there was a reason for keeping) was hollowed out to fit the outside of the bearings. The inner part of the nylon was drilled out and the hose barb was screwed in.
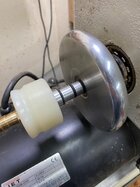
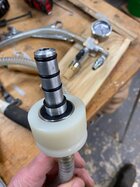
Fittings, gauge and valve purchased and fitted together with PTFE tape and off we go. Used a sintered exhaust silencer as a filter below the quarter turn valve and then this was attached to the lathe using one of the belt cover bolts, which makes it easily removable.
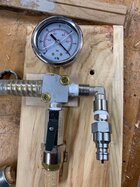
Very poorly produced video making the adapter (and you'll be able to find others on the manifold and chuck)
Adapter Video
More chucks to make. further details to follow.