I have had this burl for more than 10 years. I took a woodturning class in (I think) 2011 and roughed it out green then. I never finished it mostly because I never figured out a plan for the voids. They are from digging out some very soft wood (I think cambium). Inside the bottom of the bowl there's some knotholes but those are easily filled with epoxy. I wanted to leave the voids but I think they're too big and the piece will fly apart when turning. At it's deepest its about 3/4 deep. There is one on the other side that doesn't hit the rim or the bottom of the bowl. At some point in the past I started filling it with blue resin (looking back that was a mistake IMO) so I may try to drill and chip it out. If I can't, I will figure out something similar for this side and live with it. Could I do something like turn the rim flat and then glue on a solid piece to hold the top of the rim together? Then figure out a creative way to stitch wood across the voids?
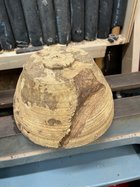
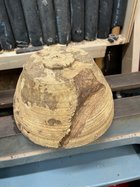