This is a "sort of" goblet that I have been sweating over for the last two days. Totally new to inletting or hollowing end grain or any grain, for that matter. Need to work on some of my interior technique as I left some tool marks. Posting a photo as how to part off part of the base on the left side. Plus, I want to recess the base a bit so it will sit straight. Best way to part? How to hold the piece to recess the base? Many thanks to the forum!
Walt Wager was most helpful in getting started. Mike Waldt has a video that expanded on using various tools for inletting end grain. Thanks to both!!!!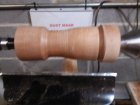
Walt Wager was most helpful in getting started. Mike Waldt has a video that expanded on using various tools for inletting end grain. Thanks to both!!!!
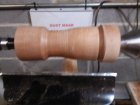