The good and bad of Saturday turnings.
The good: After the hurricane some one brought me a piece of maple and chestnut and ask if I could turn four bowls to auction off and give the money to artist that lost everything in western NC. I agreed and did the second turning Saturday morning on two of them. I hated turning the green chestnut on the first turn, the sticky sap stuck to everything including me! The dry chestnut turned great. I left the hole in the maple to represent the hole left in communities from the hurricane. I’ll turn the other two later.
Also, had some small maple pieces and turned a couple of natural edge to try second turning them in a few months, usually just once turn natural edge bowls.
The bad:
My wife reminded me we were going to Piegon Forge TN for a few days. If anyone is in Piegan Forge next week I’ll be the guy sitting on the bench outside the stores looking dazed and confused. She did agree to let me go hiking one morning
.
Put a fresh piece of a new maple log on the see what this log would look like and to see just how thin I could turn it. Practicing for a cowboy hat in the near future. Had a light behind it, was paper thin, loosened the chuck, didn’t get it open enough before I tried to take the piece out, edge of the tenon caught on the chuck and two fingers went through the side of the bowl, then it was hammer time
. Can’t remember the last time I went through the side or bottom of a bowl but at least it wasn’t with the gouge!
Immediately grabbed a smaller dry walnut bowl to second turn a closed rim bowl. Was looking good and making the final transition near the bottom. I usually turn my air compressor off when concentrating on certain turnings but forgot. Right as I touched the gouge to the transition area the air compressor kicked on, I jerked and messed up the transition, could fix it to my satisfaction, so finished the bowl and will give away and not sign
. Wife couldn’t see it but I could feel it and will not sell something that doesn’t pass my inspection.
So, maybe a few days away will do me some good
!
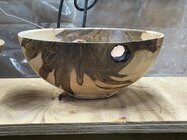
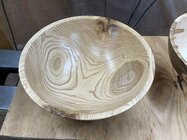
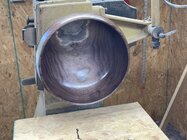
The good: After the hurricane some one brought me a piece of maple and chestnut and ask if I could turn four bowls to auction off and give the money to artist that lost everything in western NC. I agreed and did the second turning Saturday morning on two of them. I hated turning the green chestnut on the first turn, the sticky sap stuck to everything including me! The dry chestnut turned great. I left the hole in the maple to represent the hole left in communities from the hurricane. I’ll turn the other two later.
Also, had some small maple pieces and turned a couple of natural edge to try second turning them in a few months, usually just once turn natural edge bowls.
The bad:
My wife reminded me we were going to Piegon Forge TN for a few days. If anyone is in Piegan Forge next week I’ll be the guy sitting on the bench outside the stores looking dazed and confused. She did agree to let me go hiking one morning

Put a fresh piece of a new maple log on the see what this log would look like and to see just how thin I could turn it. Practicing for a cowboy hat in the near future. Had a light behind it, was paper thin, loosened the chuck, didn’t get it open enough before I tried to take the piece out, edge of the tenon caught on the chuck and two fingers went through the side of the bowl, then it was hammer time

Immediately grabbed a smaller dry walnut bowl to second turn a closed rim bowl. Was looking good and making the final transition near the bottom. I usually turn my air compressor off when concentrating on certain turnings but forgot. Right as I touched the gouge to the transition area the air compressor kicked on, I jerked and messed up the transition, could fix it to my satisfaction, so finished the bowl and will give away and not sign

So, maybe a few days away will do me some good

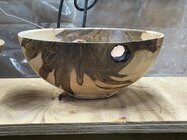
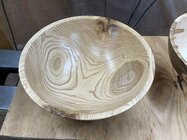
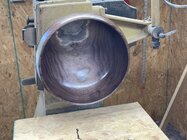
Last edited: